New robotic cell for current testing and laser marking of KZS-2M/4M RCBOs
At ETI, we continue with the automation of production processes. The new robotic cell for current testing and laser marking of KZS-2M/4M RCBOs is one of the first automatic assembly / testing robotic cells in our switchgear department. With its introduction, we have successfully replaced manual retesting, laser marking of RCBOs, assembly of the snapping unit, sealing of the adjustment screw, and insertion and testing of the test button. With the new device, only the code of the product is entered, and in accordance with the previously created program and laser marking design, the device will perform the necessary operations to produce the final form of the RCBO.
Andraž Pušnik |
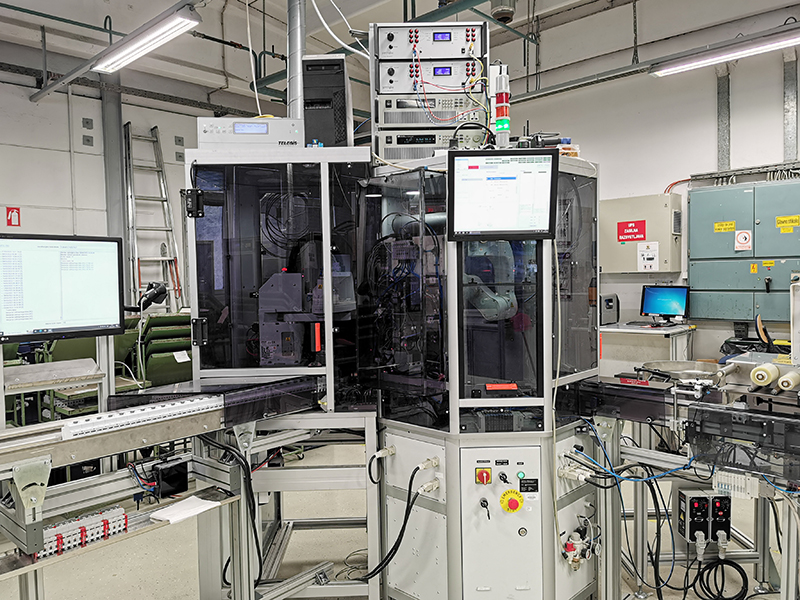
The new robotic cell for current testing and laser marking of KZS-2M/4M RCBOs works according to the following procedure: The first step is to insert the products onto the conveyor belt of the device, which remains manual. After insertion, the electrical characteristics of the RCBO are tested, which is automatically carried out in two special measuring cavities, ensuring the autonomy of the device. The device is capable of testing all types of KZS RCBOs for type, rated current and rated residual current. The next step is laser marking, which is activated only if the measured electrical characteristics of the RCBO conform to the norm. The front marking, side marking and date code are laser printed onto the RCBO. This is followed by the sealing of the adjustment screw, which the device performs automatically with the paint dosing system and the respective dosing needle. The installation of the snapping unit is the next step, where snappers are automatically brought to the device and the device snaps them to the bottom of the RCBO with a special mechanism. The penultimate step is the pad printing of the chosen logo, which is done with an automatic pad printing machine while the RCBO is already moving along the conveyor belt of the output line. At the end, the worker packages the RCBO.
The big innovation is the laser marking method. The previous time-consuming pad printing and color adjustment on a pad printing machine has been replaced by a laser system. With the laser, it is possible to write on various surfaces, insert arbitrary characters, and the indelibility of the data is guaranteed. In our laser system, the lens is fixed and we change the orientation of the RCBO with the robotic arm. In this device, we also add a date code to the product, which contains the date of manufacture, to make it easier to track changes. All three steps of laser marking together take about 4 seconds, although this time varies depending on the amount of data being written. Each RCBO contains a DMC code on the lower part, which enables the traceability of all measurements and the repetition of passes through the device.
KZS-2M RCBOs on the output conveyor belt of the device
The innovation has helped improve productivity, quality and traceability. The machine is designed to be able to process products faster than was previously possible with manual processing. As a result of automation, we have also achieved better repeatability of the process, which increases product quality.